U.S. manufacturers are likely to feel some shifts within federal laws, regulations and enforcement over the next few years. What can they do now to adapt and prepare?
As of Jan. 1, the U.S. increased tariffs on Chinese solar wafers and polysilicon imports (to 50%) and for certain tungsten products (to 25%). Tariffs are likely to increase further under the incoming Trump administration. “Many manufacturing companies have been telling me their biggest concerns are tariffs,” said Grant Thornton Manufacturing Industry National Leader Kelly Schindler. “During the campaign, we heard President Trump talking about significant tariffs for China and on imports across the board. That will mean a cost increase for our manufacturing clients; for many, it could be quite substantial.”
President Trump’s 2024 campaign and first administration indicate that manufacturers could see:
- Sector tariffs that continue or expand existing measures, like the 25% tariff on imported steel and 10% tariff on imported aluminum
- Chinese import tariffs of at least 60% on a range of goods
- Targeted tariffs on automotive imports from Mexico of as much as 100%
- Universal tariffs of 10–20% or more on all imports
These tariffs have been discussed as a means of promoting domestic manufacturing, but they could also lead to supply chain disruptions for manufacturers that depend on imported goods. “We don’t know what the tariffs are going to be, or on which commodity, or how those countries will respond, but that doesn't mean we can’t do things to mitigate any impacts now,” said Grant Thornton Growth Advisory Services Principal Jonathan Eaton.
While manufacturers might not know the impact or ultimate timing of potential policy changes, they can still take action to proactively mitigate risks and help ensure business resilience. To do that, they need to understand potential scenarios — there are many changes that could have positive or negative impacts on individual manufacturers.
Understand potential changes
Beyond tariffs, manufacturers should consider potential changes in health regulations, environmental restrictions, energy policy, labor, immigration and taxes. Tax changes could be the top reason to re-examine your investments and business strategies.
Taxes
“Taxes have been a big concern for manufacturers and the National Association of Manufacturers for all of 2024, seeking an extension of important provisions from the Tax Cuts and Jobs Act,” (TCJA) Schindler said.
“I would say that, overall, Republicans are very supportive of many provisions in the Tax Cuts and Jobs Act,” said Grant Thornton Public Policy and Government Affairs Manager Austin Sevage. Manufacturers will be urging Republicans to not only extend favorable provisions expiring at the end of 2025, but to restore the ability of businesses to fully expense research costs and investments in equipment. “Timing might be something to consider,” Sevage said. “It could go toward the end of the year that any extension ends up happening.” Congress will use the reconciliation process to pass a TCJA extenders package, which will likely include provisions on border, energy and defense as well. Everyone will be monitoring how quickly this will get through in some form or fashion.
Another consideration is a potential 15% tax rate for domestic production manufacturing, which was discussed during the U.S. presidential campaign. “This could be difficult to actually get implemented,” Sevage said. However, we could see changes if a consensus builds behind the enactment. Republicans in Congress will need to demonstrate how those lost tax revenues will be replaced. Beyond taxes, manufacturers are also monitoring other critical initiatives.
Semiconductors
Semiconductor supply chains became a hot issue with the chips shortage during the pandemic, which is why the 2022 CHIPS Act allocated funding for U.S. microelectronics research, fabrication, training and overall supply chain security. Congress is very supportive of the CHIPS Act, Sevage said, so he expects the CHIPS Act to continue fostering U.S. semiconductor development.
The CHIPS Act, and the January 1 tariff increase on semiconductors from China, mean that manufacturers should look for ways to start taking advantage of domestic semiconductor development. “Those within the national security community, and within the economic security community, recognize the importance of developing a domestic supply chain for microchips,” Sevage said, adding that the balance of incentives and tariffs could work together to incentivize domestic manufacturing. “I could see that framework being used for other critical items as well.”
Critical minerals
U.S. manufacturers should also foster alternative supplier relationships for critical minerals, in case other nations restrict shipments of these items in the context of trade negotiations. China recently announced another ban of further critical mineral exports to the U.S., targeting minerals essential for aerospace and defense production.
Sevage said that the first Trump administration acknowledged the need for domestic supplies of critical minerals, and ordered a study of the issue. Since then, federal funding has helped to build the domestic critical mineral supply chain. “So, in the long run, the U.S. is moving toward less reliance on China and other external sources for critical minerals,” Sevage said. “At one point, the U.S. was the largest producer of these minerals. China used some market forces and non-market forces, like reduced regulation and government subsidies, to start producing them much cheaper.” Accordingly, the incoming Trump administration intends to relax regulation and permitting in the U.S. on the extraction and production of critical minerals so that these can again be a supply chain option for domestic production.
“China’s recent action only proves the point that we can't be reliant on China for these minerals that are elements of national security and economic security,” Sevage said. “These are also potentially another bargaining chip that China can use in trade negotiations with the Trump administration. So, I would expect that this is just a step on that escalatory ladder and there is likely more to come.”
Health regulations
President Trump’s nominee for U.S. Secretary of Health and Human Services, Robert F. Kennedy, Jr., has indicated that he might support policies that would affect food and beverage makers. “There has been discussion of banning various food colorings and sources of food coloring,” Eaton said.
“The Make America Healthy Again initiative is causing some concern with our food and beverage clients that manufacture additives or preservatives, or use them as ingredients in their products and don't have an organic option,” Schindler said. Eaton said that some food and beverage makers should assess alternate ingredient scenarios for each food product produced, to evaluate possible product exits and where products can be altered without significant cost — as well as their ability to track complete data about ingredients in the products.
“I have food and beverage clients that can tell you exactly which lot it was, where it came from, how much of it was used or even if it has an ingredient that was bought from someone else,” Eaton said. If health regulations draw new lines around ingredients, companies and regulators will increasingly depend on this level of detail to identify, plan and prove the ingredient lists in every product.
Environment
In March 2024, the U.S. Securities and Exchange Commission (SEC) adopted new rules that require annual reports and registration statements for publicly traded companies to include information about the company’s greenhouse gas emissions and other environmental impacts.
President Trump has nominated former SEC Commissioner Paul Atkins to become the SEC chair, and “Paul Atkins was already vocal about undoing this SEC rule when it happened,” Sevage said, adding that most or all Congressional Republicans oppose the rule. “So, it will be undone, but there are a few paths. In his first 100 days, President Trump will probably try to take some actions through executive orders to reduce enforcements, but this is a final rule. So, ultimately, it could take up to several years to undo this through the standard APA process. One alternative path is that this rule is currently being challenged in the courts, and there's a stay on it. The Trump administration could choose how they continue to argue that. If the rule is vacated by a court, they might just take that loss and rack it up as a win that the rule gets vacated.”
Aside from the SEC’s rule, manufacturers that have production in California or Europe also need to consider the stricter environmental regulations in force there. “As California and the EU are leading with strict regulations, that's probably going to set the tone for most companies. I think that most companies will comply with the strictest regulation,” Sevage said. Sevage added that EU Corporate Sustainability Reporting Directive (CSRD) environmental regulations could be another negotiating point in trade discussions. “In the first Trump administration, part of tariff and trade talks focused on regulatory barriers to market access in Europe. Those regulations might become part of a future trade deal.” Any change could take considerable time, however, so companies should not slow their CSRD reporting initiatives.
Energy
Environmental issues often tie into energy policy discussions, especially in the balance between fossil fuels and renewable energy. The Trump administration could tip that balance back toward fossil fuels. “I think it can be summed up in the idea of ‘Drill baby drill,’” Sevage said. “The Trump administration will be highly focused on opening up the ability for domestic producers to expand their operations.”
Sevage cited the choices of North Dakota Governor Doug Burgum as Secretary of the Interior and Chris Wright as the Secretary of Energy, saying “I think the general idea is all energy is good energy, and they want to reduce costs across the board.” Sevage added that there was bipartisan support for the Energy Permitting Reform Act of 2024, which streamlined the permitting process for energy projects across the U.S. “Republicans look at that from the perspective of loosened regulations that make it easier to qualify for permits, and Democrats look at that from the perspective of getting new renewable projects online. Overall, I think both sides are looking to make this happen.”
Legislators might be driven by concerns about the nation’s energy infrastructure. “The manufacturing industry is the largest user of energy in the United States,” Schindler said, “and current statistics show that, in the next few years, the grid as it currently stands will not be able to support all the energy consumption needed by domestic manufacturers.” More energy production and producers could support growing demands and decrease the energy costs that have been a budget burden for manufacturers.
Immigration
Many workers who are undocumented, or still in the process of documentation, play a role in manufacturing. They work directly in the industry, or indirectly in supply chains like the agricultural production of ingredients, extraction of minerals or production of oil.
Eaton said that stricter immigration enforcement could have both direct and indirect impacts on manufacturing. “I think it could really disrupt supply chains, and the ability of a manufacturing company to thrive and deliver on its commitments. I work with manufacturers every day that are struggling to fill jobs, and are battling to keep people who’ll change jobs for 10 or 20 cents more per hour,” Eaton said. “It's become extremely problematic, especially in manufacturing environments that require heavy protective safety gear, have hot or undesirable working conditions, or where work is very labor intensive. There are other jobs available with better working conditions that pay the same and offer a clearer path to upward mobility.”
Once manufacturers understand the range of potential changes that could affect them, they need to identify their risks and get ready to adapt to different scenarios. “Companies must understand where they have exposure today, think about their options, evaluate those options, then put plans in place now,” Eaton said. To help address labor costs and skill gaps, manufacturers should look at technology modernization and automation. The unintended upside is that employees exposed to technology can grow professionally and stay because of opportunities for learning and advancement.
Find risks
What can companies do now to prepare for the potential impacts of changes in federal policies and enforcement? “Several things come to mind,” Eaton said:
Revenue analysis
Companies must analyze their revenue to re-prioritize and adapt their strategies if new policy changes could negatively impact revenue. Eaton explained, “To do this, manufacturers should know exactly where their revenue comes from as it relates to customer segments, channels, markets and other variables, along with where the gross margin is — where the money is really made, and which customers are vital for sustainable and profitable growth.”
“Understand your customers and customer segments that are critical and strategic to the overall revenue goals of the company,” Eaton said. Update this analysis now to help you see where you have room to extend price increases, or where looming policy changes might make it practical to pursue new customer segments, contract models or suppliers — or even where you might gain a competitive advantage that you didn’t have before.
Supply chain analysis
An updated revenue analysis can help you quantify the complex factors in your pricing strategy, and that also informs your choice of suppliers. “You should trace back and analyze, for the products that you sell, which ones are your priorities, and who the suppliers are for those raw materials and intermediates,” Eaton said.
“Understand where those products are made, what goes into them and what your options are for alternative sources of supply,” Eaton said. With this analysis of your supply chain, you can be prepared to re-balance your suppliers if policy changes make some partners more practical, less practical or entirely unavailable.
Risk analysis
When you analyze your revenue, supply chain and other areas of your business, you will find risk exposure. Eaton said manufacturers should analyze risks now, to inform how they can mitigate them presently or manage them in the future. “Maybe it's a commodity going into your products — do you have an alternative source of supply, and how did you handle it the last time there were tariffs? Is that still an option? Did those suppliers raise prices, and is there a way you could pass that along to your customers?”
“The unfortunate reality with alternative sources of supply is that other companies are going to be seeking the same,” Eaton said. “So, the demand is greater than the supply, and the price goes up in a different form.” By identifying your risks and considering the likely impacts now, you can proactively plan different scenarios to prepare for quick and competitive action.
Explore scenario planning
With an updated business analysis, you can define scenarios and evaluate each one to help ensure you’re ready to take action with insight, preparation and speed.
“The essential thing that companies can and should be doing today is scenario planning,” Eaton said. “You should have executive teams saying, ‘Here's the particular failure mode or scenario and, if this happens, what are we going to do?’ Think about your options — none of them will be silver bullets, but at least have options. Think about how specifically you would handle a situation and assess your company’s readiness to execute if required.” Each of your possible options could involve trade-offs and complexities that are important to discuss ahead of time.
“Work through that at a product level and a customer level,” Eaton said. Manufacturers are both producers and customers in their supply chains, and Schindler emphasized that tariffs can have an impact on both ends. “We could have tariffs on the importing of goods used by our manufacturers, as well as retaliatory tariffs that have an impact on a manufacturer’s sales into other countries,” Schindler said. Eaton agreed, “I would not be surprised if that happens.”
As you identify your risks, plan options for scenarios and weigh the factors involved, you can better prepare to take action in the future — but there are some actions you should take today.
Take action
Your risk analysis and scenario planning can inform actions that you should take today — like building the relationships required for your scenario plans. “When you think about the things that you would potentially do, you can see the conversations that leaders need to be having today,” Eaton said.
- Production:
As you look at the bill of materials for each product, review your current suppliers and consider alternatives, you might need to start laying the groundwork for those alternatives. “Think about where you would get another supplier, start to vet the suppliers, and start to have those conversations about getting pricing and agreements in place.” By having these conversations now, you can improve your company’s position if and when you need to act on your alternative scenario plans. - Labor and technology:
You might also need to initiate discussions about potential workforce changes, including impacts from technology initiatives. Federal policies might not affect your technology initiatives, but those policies might push you to adopt scenario plans that include technology solutions quicker. Consider where you need to discuss those options now. “When working with unions, first and foremost you need to understand and respect their position,” Eaton said. “Technologies like robotic process automation and artificial intelligence offer very real capabilities, and these capabilities do not have to eliminate the job or eliminate the need for people. Bring workers along, let them be a part of the process, and talk about how a given technology would improve the job, how it changes job design, and how it changes the need for certain types of jobs.” It's important to plan workforce training and promotion paths at the same time you are considering technology initiatives. “Talk about providing training and opportunities for advancement or more earnings for the people who adopt these solutions — those early adopters and champions are going to be so critical for effective change management. Have that conversation with the union in a non-adversarial way that respects the perspective of the employee but also communicates in a transparent way.”
To truly build resilience, you need to lay the groundwork for the scenario planning that you’ve done.
“Good risk management entails understanding how you can achieve business continuity and resiliency, along with identifying the risk factors that could hinder your success,” Eaton said. “You need good discipline for scenario analysis and planning, to identify the options and have a playbook that says, ‘Here's the trigger. If the triggering event occurs, these are the actions that we take,’ as opposed to being caught flat-footed and having to decide how to react after the fact. What I have been telling everyone is to focus on what to do when, and identify the things that you can do now.”
While you might not know how factors will change, now is the time to update your understanding of the factors in place today and the options you can take.
Contacts:
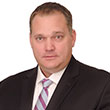
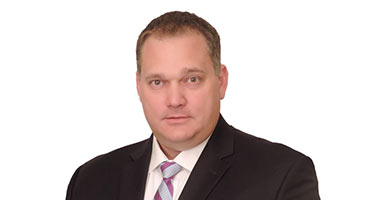
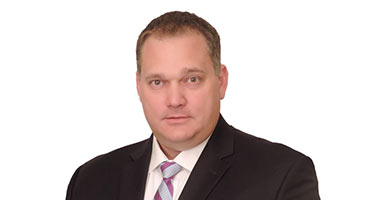
Jonathan Eaton
Principal, Business Consulting
Grant Thornton Advisors LLC
Jonathan is a Principal in the Operations & Performance practice.
Charlotte, North Carolina
Industries
- Manufacturing, Transportation and Distribution
- Technology, Media and Telecommunications
- Energy
- Retail and Consumer Brands
Service Experience
- Advisory Services
- Business Consulting
Content disclaimer
This Grant Thornton Advisors LLC content provides information and comments on current issues and developments. It is not a comprehensive analysis of the subject matter covered. It is not, and should not be construed as, accounting, legal, tax, or professional advice provided by Grant Thornton Advisors LLC. All relevant facts and circumstances, including the pertinent authoritative literature, need to be considered to arrive at conclusions that comply with matters addressed in this content.
Grant Thornton Advisors LLC and its subsidiary entities are not licensed CPA firms.
For additional information on topics covered in this content, contact a Grant Thornton Advisors LLC professional.
Share with your network
Share